Zastosowania i zalety cięcia laserowego aluminium
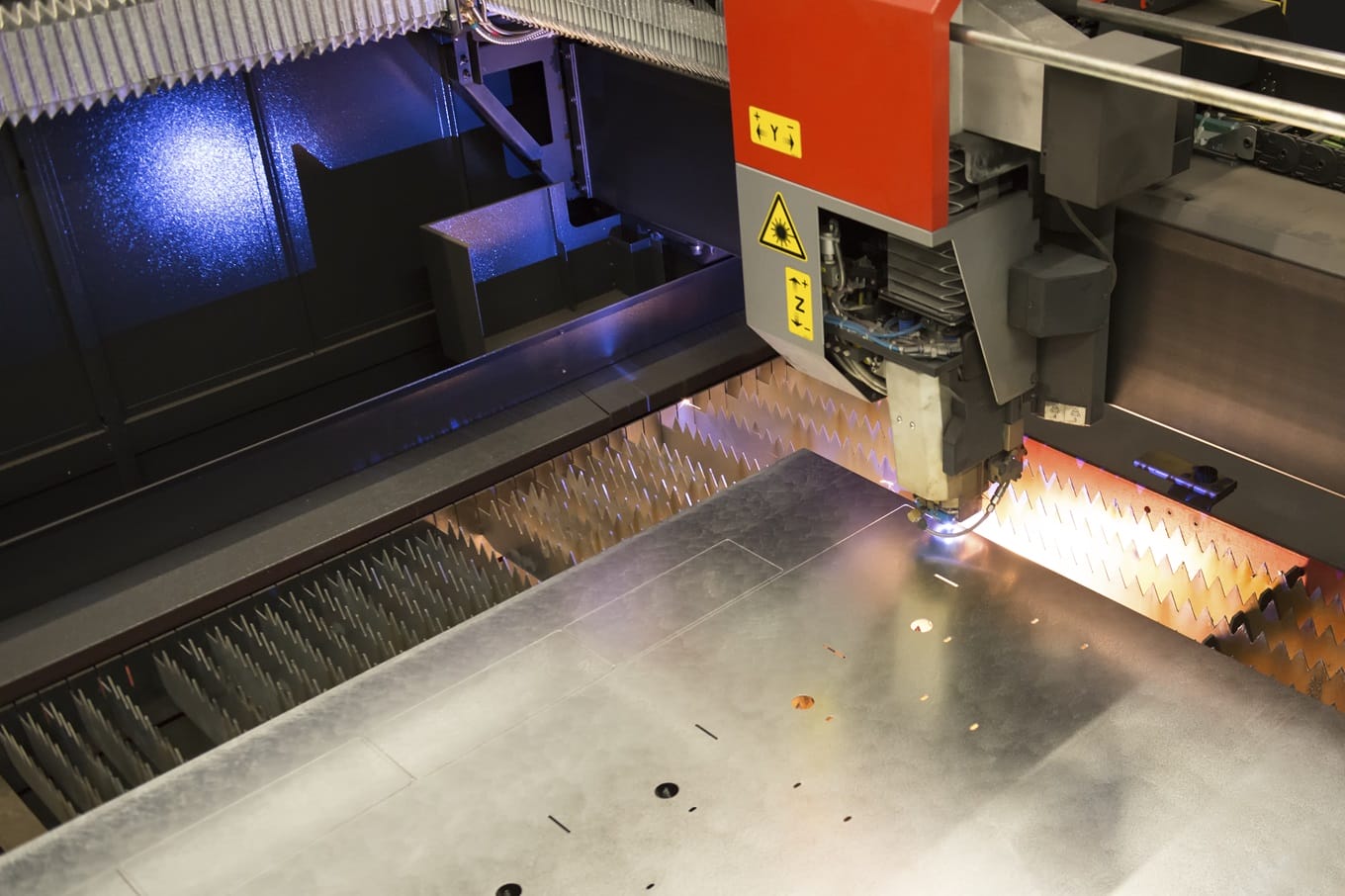
Laserowe cięcie aluminium rewolucjonizuje obróbkę tego lekkiego, a zarazem wytrzymałego metalu, oferując precyzję i wszechstronność w wielu branżach – od motoryzacji po dekoracje wnętrz. Jeśli chcesz dowiedzieć się, jak laserowe cięcie aluminium może usprawnić procesy produkcyjne i jakie korzyści przynosi, zapraszamy do lektury – przybliżymy Ci techniczne aspekty i praktyczne zalety tej nowoczesnej technologii!
Technologia cięcia laserowego aluminium
Cięcie aluminium laserem wykorzystuje wiązkę lasera CO2 lub światłowodowego o długości fali 1064 nm, która topi i odparowuje metal w punkcie kontaktu, wspomagana gazem technicznym (azotem lub tlenem) o ciśnieniu 10-20 barów, usuwającym stopiony materiał. Proces pozwala na obróbkę blach o grubości od 0,5 mm do nawet 20 mm, zależnie od mocy lasera (zwykle 2-6 kW) i rodzaju stopu aluminium (np. 1050, 5083). Kluczowa jest tu precyzja – tolerancja wynosi ±0,1 mm, a krawędzie są gładkie, bez zadziorów, co eliminuje potrzebę dodatkowej obróbki. Laserowe cięcie aluminium jest idealne do produkcji powtarzalnych elementów o złożonych kształtach, minimalizując straty materiału.
Zastosowania w różnych branżach
Laserowe cięcie aluminium znajduje szerokie zastosowanie dzięki swoim właściwościom – lekkości (gęstość 2,7 g/cm³) i odporności na korozję. W motoryzacji używa się go do wycinania elementów karoserii czy ramek. W budownictwie sprawdza się przy produkcji elementów elewacji czy balustrad. Branża reklamowa korzysta z tej metody do tworzenia szyldów i liter 3D, a dekoratorzy wnętrz wycinają z aluminium ażurowe panele czy ozdoby. Dzięki wszechstronności i precyzji laserowe cięcie znajduje także zastosowanie w elektronice, produkcji sprzętu AGD oraz w przemyśle meblarskim, gdzie liczy się estetyka i dokładność wykonania.
Zalety cięcia laserowego aluminium
Główne atuty laserowego cięcia aluminium to precyzja, szybkość i elastyczność – wycinanie skomplikowanych wzorów, jak kratownice czy otwory o średnicy 1 mm, jest możliwe bez użycia dodatkowych narzędzi. Technologia redukuje odpady dzięki wąskiej szczelinie cięcia (0,2-0,5 mm), co obniża koszty materiału – np. z arkusza 1000x2000 mm wycina się więcej elementów niż metodą tradycyjną. Brak kontaktu mechanicznego minimalizuje ryzyko odkształceń, a wysoka powtarzalność (do 99,9%) gwarantuje identyczność detali w seriach. Proces jest też ekologiczny – zużywa mniej energii niż cięcie plazmowe (ok. 10-15 kWh na godzinę) i nie wymaga chemikaliów. To rozwiązanie, które łączy wydajność z nowoczesnym podejściem do obróbki metalu.